During Asbestos Awareness Week 2009 in Melbourne Australia the trade union movement pledged to begin a national strategy to control and remove asbestos from Australia. This would have been a very tall ask any time in the last two decades but Asbestos needs to compete now with Climate Change for the attention of the media, the decision makers and the heartstrings of the community.
It is accepted that in the near future more people will be touched directly and indirectly by asbestos-related diseases but, at the moment, the issue is concentrated in low-income industrial suburbs and, as such, is still dismissed by some (often in suburbs with large trees and no pubs) as a disease that only strikes the blue-collar smokers. The social inequity of asbestos-related diseases should be studied in some depth as it is likely to shame governments into action on this hazard.

At a seminar in late November 2009, a small audience in the Victorian Trades Hall was told of the success of the Tasmanian campaign in gaining government support for the removal of all asbestos by 2030. Jim Ward of the Australian Workers Union spoke of the approaches to Goliath Cement (“The James Hardie of Tasmania”). Ward told how the CEO of Goliath did not blink at the request to remove asbestos. Ward said this type of response has been repeated throughout Tasmania.
The audience also heard from several who are at the frontlines of dealing with asbestos-related diseases. Vicki Hamilton and Tim Tolhurst spoke of the frustration of having inadequate disposal facilities in regional areas of Victoria. The challenge here is immense as the temptation to bury asbestos in the back paddock when no one’s around is strong even though it is selfish and immoral. Vicki and Tim showed how a structured program across the community is required because one cannot encourage the removal of asbestos until there is a place to safely dispose of it.

Pat Preston, ex-CFMEU and now with the Asbestos Contractors’ Group, spoke of the legislative and operational problems faced by licensed asbestos removal contractors. The holes and conflicts all complicate the process of asbestos removal and disposal and increase the cost, particularly of asbestos removal.
Several speakers pointed to the anomaly that the removal of asbestos from domestic buildings of less than ten square does not required licensed removal, thereby “encouraging” small volumes of asbestos to be hidden at the bottom of domestic rubbish bins. The OHS risks to waste collectors are not dissimilar to those who dispose of toxic and trade waste down the toilet next to the workshop when WorkSafe or the union is not around.
Of course the audience and speakers seem to all agree that there is no safe level of asbestos exposure. There are certain to be those in Australia who are “asbestos-skeptics” and many seem to have the ear of the decision-makers.
One speaker provided a fresh perspective that was very appropriate but surprising for a couple of reasons. Anthony La Montagne, of the University of Melbourne, has undertaken ongoing research on job stress, cancer clusters and, clearly, asbestos issues. La Montagne provided the glum news that several promising medical techniques for early detection of asbestos have come to nought. The only effective risk reduction technique is for those who may have been exposed to asbestos to quit smoking as this smoking appears to exacerbate asbestos-related disease.
Several speakers noted that in the Asbestos Awareness Week 2008, there was a motion to have the Government undertake action on asbestos. The resulting inaction was embarrassing and motivating with participants committing themselves to continuing to lobby for controls on asbestos. This is going to be a considerable challenge if they continue through the same lobby process that they have applied for the last few years.

The asbestos safety advocates should drop “awareness” from the week’s title because awareness equates to “aspirational targets”, former Prime Minister John Howard’s way of promising much and delivering nothing. Just as everyone accepts that smoking causes lung cancer and climate change exists, people know that asbestos can kill. Move away from awareness-raising to action.
Research the social inequity of asbestos in low-income areas. Many domestic houses have asbestos houses or in their roofs, particularly in low-income areas which are also the areas where asbestos workers live. If the reality and scope of this situation was proven to a level and in a format that policy-makers accept, the asbestos control option would be much stronger. Even if the government continued its inaction, a case could be put to the discrimination tribunals and human rights sector to shame the government to represent all citizens equally.
Market the asbestos week. White, pink and striped ribbons are becoming a fundraising cliché but the marketing of social health issues works. There must be a coordinated approach to getting sponsors and support into the promotion of asbestos-related diseases on a large scale. Once there is serious money behind the issue, one can fund research and present data that convinces decision-makers of the reality of the issue.
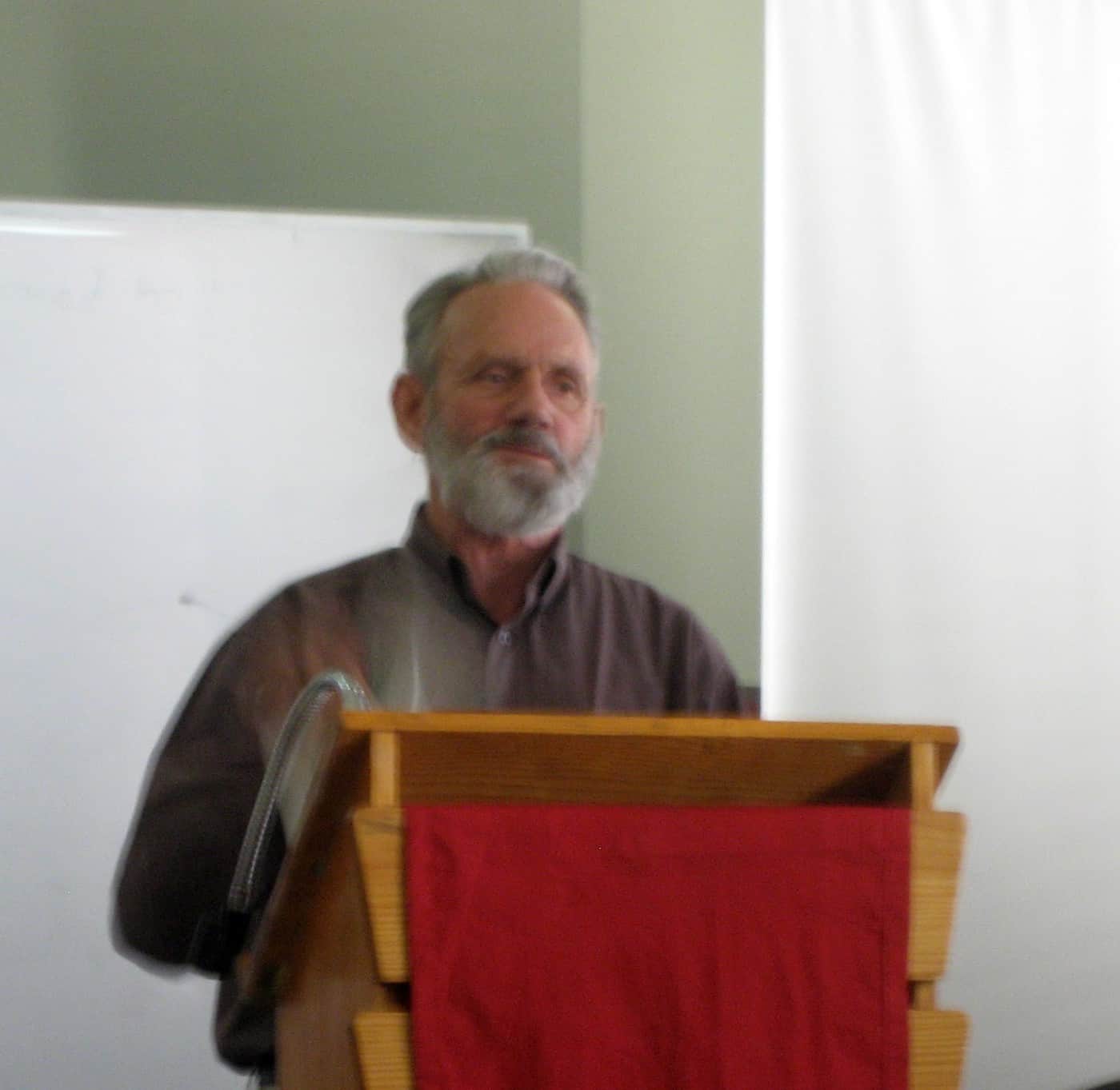
Undertake a public health cost-benefit analysis of asbestos-related disease, as one speaker advocated at the Victorian Trade Hall. There are many lessons from the compensation issues of James Hardie Industries but one is that compensation creates wealthy (for a short while) families of dead workers and can do little of health benefit to the mesothelioma sufferers. It is surprising that the fact has not clicked in the government mind that compensation for asbestos-related diseases provides an important but only symptomatic relief. The government is applying paracetamol to an issue that requires surgery.
The union seminar was heartening in that it showed how many people are actually tackling the issue of asbestos-related diseases. But it also operated under a cloud of frustration with an occupational and public health risk that is not receiving the government support that other similar matters are. Trade unions are a vital part of any plan to control asbestos but just as many people in the leafy suburbs are isolated from asbestos risks, so the audience for the asbestos message is limited by the message remaining within the trade union context.

There needs to be a creative approach to generating sufficient community outrage over the unnecessary deaths of workers from asbestos so that the government cannot avoid action. The James Hardie legal action and the lobbying of Bernie Banton, and others, was about compensation, about making a company accept its social responsibility, about making it pay. It worked, but James Hardie still cannot afford the compensation bill that is the reality of decades of profits from a toxic substance that kills.
In 2009 several Australian Governments have helped out this company by contributing $A320 million to the company’s compensation fund. Why? When did the government decide to cover the costs of a company’s exploitation of workers? This is on top of having to fund the public hospitals that have to deal with mesothelioma victims. The government, and the taxpayer, is paying twice!
Let the company fail and allow the class action lawyers to pick over the assets. Or better yet, keep James Hardie Industries alive and bleed it just enough so that it can fund the removal of its toxic legacy for the next thirty years.
Every shareholder in James Hardie that receives their dividend cheques from whichever country James Hardie moves to next (Zimbabwe cannot be far off) needs to understand that those dividends could be used to ease the pain of the workers who generated the corporate profits rather than contribute to their own bloated share portfolios.