Dr Yossi Berger of the Australian Workers Union has been reading some of the debate in SafetyAtWorkBlog and offered the article below for publication. He said to SafetyAtWorkBlog
“…in relation to BP’s OHS catastrophes and comments about their management style, their managers and this aspirational, easily-bandied-about notion of workplace culture. Two things stimulated me to put together this comment below: first, on the back of some 2000 workplace inspections across Australia and some internationally I have not detected this thing called ‘workplace culture’ other than as a cheap metaphor and ploy to manipulate; even if you chose to think of this phenomenon as ‘shared values and how we do things here’. Secondly, there’s terrible and dangerous bullshit going on in relation to ‘personality cult’, ‘disconnect’ (‘no one told me’), and ‘it couldn’t happen here because we care’.”
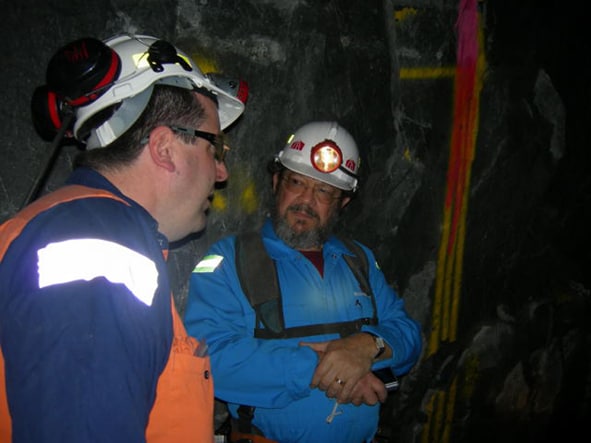
The Astonished Manager: “Not in my wildest dreams”
The distressed manager
On many sad occasions I have observed managers openly distressed after a serious incident at work (fatality, serious injury, dangerous process failure). Like with all human behaviour, their responses vary from individual to individual, but a significant set of responses keeps recurring: the following (or similar) expressions of astonishment –
- I would have never thought…[Fatality, demolition collapse]
- Not in my wildest dreams…[Molten copper explosion, process failure]
- This was totally unexpected…[Crush fatality, winery]
- Who’d’ve imagined…..?… [Forklift fatality]
- I’d have never expected…[Hand ‘granulated’]
- I can’t imagine why anyone would do that?… [Arm amputation in conveyor belt]
- How could you possibly see this happening?…[Sections of refinery closed, plant integrity]
Is such astonishment a fair and natural response after a serious incident at work?
There are circumstances where astonishment would be clearly puzzling, for example, when a soldier is killed on a battle field; when a racing driver is seriously injured at a race meeting; when a boxer is hurt in a fight. ’Not in my wildest dreams could I have predicted that you might suffer a seriously cut eye’ said to a boxer after a competition fight would be absurd.
But in which way does it make sense that in industry, generally, the manager couldn’t possibly foresee what could result from the hazards present and therefore was astonished? If something doesn’t seem right in this scenario and yet it’s accepted that the sense of astonishment is real, then either the manager is psychologically ‘at some distance’ from the reality at work, or something else is exposing him/her to the shock of the incident. Identifying what that may be could provide added understanding of OHS programs.
I’ll take the position that the manager has genuinely experienced astonishment. I’ll suggest that clues for an unusual explanation are nested within the very expressions of it. I believe that in an important part, it’s a result of restricted imaginative efforts during various forms of hazard identification, and – critically – inaccurate naming of hazards.
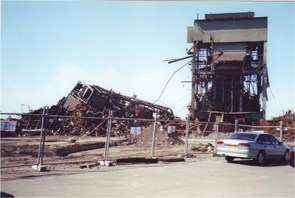
Arguments against post-incident astonishment
The following four sets of observations suggest that the manager could not have been entirely blind and unprepared for the possibility of a serious incident as to be ripe for simple astonishment, yet astonished he/she was.
The general OHS scene: It’s just not plausible that the manager didn’t have a clue and had never heard about any past OHS catastrophes in local or international industry (Beaconsfield gold mine, Longford fires and explosions, Piper Alpha, BP Texas City refinery, Moura mine disaster), where plenty of OHS management systems were in place.
OHS management systems and uncertainty: For some 30 years now several concepts and instruments have been used to structure and manage OHS programs: OHS Management Systems, Hazard Identification, Risk Assessments, various Safety Behaviour Programs, Safety Climate Programs, ‘Culture Change’, Mindfulness, various forms of Safety Case and so on. They, in turn, have provided a cautious language (e.g. ‘risk management’), explicit and implicit OHS worldviews (e.g. ‘Zero harm’) and very firmly and repeatedly suggested various uncertainties.
All of this ought to have highlighted the precariousness of OHS standards, the care that needs to be maintained, the constant OHS mindfulness and vigilant unease required, ‘Be on constant guard’ was clear. The likelihood of astonishment after serious failures ought to have been reduced, but it wasn’t.
Local OHS weaknesses: Is it the case, nevertheless, that too much trust in OHS systems had given the manager an inflated a sense of (false) safety, (‘We’re doing all we can’?) a kind of cognitive comfort zone where questions of limits, acceptable risk, responsibility and morality recede. Is it really possible that, as a result of that trust, the manager didn’t have a clue –
-
- That in fact the OHS standard was not the norm;
- That some Standard Operating Procedures (SOPs) weren’t accurate enough and that changing them was regarded by most workers as a nuisance;
- That daily work can present constant variations that are too numerous to write into all SOPs;
- That at times a short cut may appear to be the best and quickest way to do the job under various production pressures;
Generally workers’ loyalty will be to their backs and the stress of daily work, not to what they consider questionable procedures that are regularly breached and that have generated an over-zealous management particularly keen on (for example) goggles, ear plugs, respirators and safety belts. Issues that focus on personal safety and behaviour and tend to confirm the perception that management is more interested in blaming workers. Is it really possible that the manager didn’t even have an inkling about any of these?
I believe he/she knew some of these very well and it should’ve reduced the likelihood of astonishment. But it didn’t.
Legal implications: However, if a concerned manager did state openly, as a matter of course, that he/she knows that despite the local OHS program everyone, on some occasions, breached OHS procedures (short cuts are taken) and process safety (plant integrity, maintenance) had weaknesses, this is what would be implied –
-
- That to an important extent the OHS management system (and its addenda) is inadequate;
- That many procedures aren’t working;
- That training has failed in some ways;
- That supervision is inadequate;
- That the manager has failed;
- That the manager and the firm are legally exposed;
- That extra and special efforts in OHS must be attempted and demonstrated to have been attempted (due diligence), with regular evaluations and relevant monitoring;
- That a careful record ought to be kept of that extra effort;
- That any company Board ought to be fully informed and the Directors’ opinions and formal advice sought on specifics.
These create an unattractive and demeaning scenario for the manager. The likelihood, therefore, of him/her openly dealing with known hazards and short cuts is poor. It’s more likely that this generates an awkward workplace silence and further reliance on a ‘by the book’ approach, ‘We have an OHS Management System’. But the likelihood of astonishment should be further reduced (because of this knowledge – silent or otherwise); yet it doesn’t seem to be.

To visualise and to name
Therefore if the manager had heard of some OHS catastrophes in industry; knew that OHS management systems weren’t full proof; knew of local OHS breaches and possible legal implications for management he/she couldn’t, in all truth, say, ‘I had no idea at all…..none’. Work does kill and injure, and serious process failures do happen, why the astonishment?
Since the most fundamental and first step in any OHS management system, and risk assessment specifically, is hazard identification, this is the seed of later astonishment. That astonishment is not so much about the serious incident itself, but about the failure of imagination, ‘Not in my wildest dreams’. The chance discovery of a large gold nugget on a leisurely bush walk, or a very fast 3-legged rooster will generate astonishment about such an unexpected discovery in the world. But for a manager (in much of industry) to say, “Who would’ve ever thought that a serious OHS incident could possibly happen here” is absurd. Therefore, the astonishment is more likely to do with, “I just didn’t see this coming”, and that’s astonishment based on a failure to imagine. It’s about a discovery in one’s head space.
Conclusions
The explanations for workplace post-incident astonishment can be, in general terms, about a disconnect, denial and dissociation. However, the explanation offered here is that poor occupational imaginative efforts created a mind set for it – this is the under-developed skill and persistence to visualise and name (describe) the hazards meaningfully. For example,
- It shouldn’t be a ‘Hazardous chemical’, but rather, ‘200 litres of ‘fuming’ formaldehyde next to lunch room’.
- It’s not ‘No rock noise today, not at all (in the mine)’, but rather, ‘There’s an unusual dead silence in the hole’.
- It’s not ‘Detonators mismanaged’ but rather ‘Detonators repeatedly left in the open’;
- It’s not ‘Ongoing review of maintenance’, but rather ‘Mercury build up suspected in valve #1; fire risk’.
- It’s not ‘Gauges to be checked’, but rather ‘Pressure gauge 3 seems faulty; idiotic readings’;
- It’s not ’Plant integrity checks of pipes ongoing’, but rather ‘Cleaning with sea water is corroding fire fighting pipe system’.
An inappropriate ‘editing’ of the narratives at work by poor imagination and visualisation confirmed by lazy naming of hazards generated a new, artificial story about OHS standards. A ‘close enough’, or trivial, naming of hazards initiated the process of camouflage where entire sets of likelihoods, projections, risks and dangers disappeared in an increasingly opaque OHS process (the management system in totality) and encouraged the manager to develop unrealistic and more comfortable expectations. When these failed, the mental cloak was lifted and astonishment followed.
The effective horizon of OHS expectations became artificial and inaccurate, whether this was, in part, because of expediency or naiveté is another issue, but correct naming will act as a reality check and re-adjust expectations.
Dr Yossi Berger
National OHS Co-Coordinator
Australian Workers’ Union
Melbourne, Victoria
Col et al
Thanks for the wonderful contributions to this article. Please let me know if any of the SafetyAtWorkBlog articles are similarly unclear as I need to communicate well (within the parameters of defamation, of course)
Kevin
Like that Yossi\’s post points to a critical element OH&S advisors have to be constantly aware of – use direct language all the bloody time. And that is critical when it comes to written stuff.
Packing safety management system documentation with lots of nice \”safe\” words (read \”weak\” words) helps no-one. I treat \”appropriate\”, \”adequate\” and even \”competent\” as good as useless in any guidance, particularly SMS documentation for a specific workplace. If an OH&S advisor can\’t tell a client more than something or other needs to be \”appropriate\” they shouldn\’t be saying anything at all in my opinion.
Softness in OH&S language seems to have crept in everywhere. Commonly used titles for SMS documentation can have that softness.
One that got up my (substantial) nose is Central Hazard Register. I\’d plonked in the conventional title for a register I was putting together for a client. During the process I looked at the information in the register and realized the conventional title was way short of describing what the register had in it. A simple change to calling it a Hazard Source & Location Register proved to be a much more accurate title. This was even more essential given that I wanted to look at the source of hazard from the client\’s perspective, not mine. That resulted in another simple thing of grouping categories of tasks at the workplace that had a range of hazards associated with that task.
Of course, say, a forklift traveling around a warehouse creates a range of hazards, but it\’s that task the client sees as the hazard, and to boot, it does still fit very comfortably into the conventional definition of a hazard.
The example above may seem to be relatively simple, and in fact it is, but it demanded I had to shake myself out of simply joining the dots, in terms of pumping out a document that looked like the conventional type.
The big plus out of this is that the client immediately understood where the register fitted in the scheme of things. And that understanding has the effect of generating a good sense of \”ownership\” by the client and the client\’s workers.
Col Finnie
col@finiohs.com
It is not uncommon common response after a serious incident for managers to shake their heads and say \”how could this have happened? Why didn\’t we see it coming?\” while the workers will say things like \”yeah, that thing was an accident waiting to happen\” or \”we could see that coming a mile away.\”
As I regularly comment to clients, this is why, amongst the other issues Yossi identifies, vigorous, proactive and open consultation with the workforce is essential to find and the close the holes that are always there in the safety net.
Yossi has nailed it.
I too am sick of hearing these protestations of \’innocence\’. One business owner said to me \”it was just such a freak accident, no-one could have predicted this\” I was thinking \”this incident was so totally predictable, the only freak thing about it are the words coming out of your mouth\”
Every project no matter how large or small includes the cost of a workplace injury or a workplace death. Tragic but it true, the cost of a human life in dollar terms is factored into the process.
Go into a cafe and buy a ham and cheese sandwich, part of the cost paid goes towards the WorkCover levy for the cafe owner.
Take a ride in a taxi, part of the fare goes to paying the cost of the WorkCover levy.
Do the weekly shopping and part of the total amount paid goes toward the cost of the WorkCover levy.
Engage a builder to do build a toolshed or a multi-storey building, part of the cost goes to the WorkCover levy.
Every industry industry pays WorkCover levy based on the amount of risk involved and the probability of a injury through to workplace death.
So to say that injury or death is unforseen is a total lie.
All WorkCover levies paid regardless of the industry prove that the safety professionals know the risks involved and they balance the risk against money paid with the \”fingers crossed\” hope that there will never be a claim for a cut eye, let alone a workplace death.
What can I say? Dr Berger has basically said it all and it all comes down to full on punishment for transgressors who have provably failed to provide safe work environments and that should be before any \”astonishing injuries\” occur.
There are a plethora of experts in risk analysis and safety program development if an employer believes they do not have the necessary expertise to undertake the tasks themselves. I am sure the unions would also make great advisors in an ideal world, given their expertise across specific industries.
At the end of the day, the matter usually gets down to the basic \”avoid any costs we can get away with\”. I am sure that things would change dramatically if workers compensation insurance was not available and employers were responsible for all rehabilitation and ongoing costs directly.
All in all, a very thought provoking article that exposes the lack of honesty in the OHSW space generally, which in effect, leads to where we are today and that is not a very good place at all.
I have had the opportunity to read this article several times since Yossi emailed it through. There is a lot of truth to digest but I was particularly taken by
\”…the process of camouflage where entire sets of likelihoods, projections, risks and dangers disappeared in an increasingly opaque OHS process… and encouraged the manager to develop unrealistic and more comfortable expectations.\”
OHS consultants and professionals may need to re-examine the advice they provide to clients to ensure that safety improvement is being achieved in reality. It is easy to fall into an advisory routine that one provides to client after client after client. Safety advice can become a habit and habits need regular review to see if the action can be applied in a fresh way.
Over the last month, I have heard one international safety expert say that we should not \”dumb-down\” safety management to our clients as, in the process, we are also dumbing-down the OHS profession. Yossi seems to be saying that safety management can be complex and that there is a lot of safety research, but that that context should not impede the Plain English advice that we should provide.
I wonder whether safety professionals are providing the material that is being for the camouflage and distraction.